*This is a Washington State average for this occupation. Wage rates vary by employer, industry, experience and location.
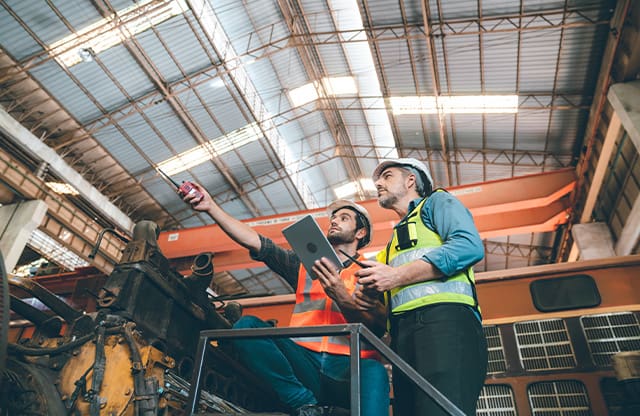
What is an Operations Specialist?
An operations specialist is responsible for the management of workflow throughout different departments within a manufacturing business.
The purpose of this position is to optimize daily activities and performance across the production floor. They are responsible for project management, staff support, meeting manufacturing deadlines, solving unusual or complex production related problems.
Operations Specialists:
- Ensure quality standards are upheld, and investigate and resolves operational issues.
- Maintain and aid in ERP software system management
- Maintain computer systems, and interpret/generate required reports.
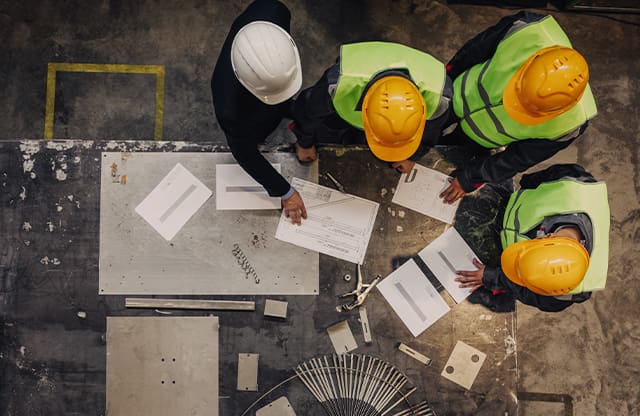
What are the Benefits of Becoming an Operations Specialist?
An Operations Specialist is an apprenticeship occupation that develops foundational manufacturing leadership skills for aspiring machinists, shop floor staff, or industrial maintenance technicians.
Upon completion of AJAC’s Operations Specialist apprenticeship, you can move onto more advanced careers including line supervisor, shift lead, operations manager, and production lead.
As an Operations Specialist, you will enjoy a long-term career with a good salary, job advancement opportunities, and the chance to lead others, work with your hands, and use cutting-edge technology.
Steps to Becoming an Apprentice


6 Steps to Becoming an Apprentice
Get Hired by a Participating Employer AJAC Partners With
Receive Participation Approval from Your Employer
Sign an Apprenticeship Agreement with AJAC
Enroll in AJAC’s Apprenticeship Classes Each Quarter
Log and Submit Your OJT Hours Monthly
Receive a Nationally-Recognized Journey-Level Certification from L&I
How Much Can I Earn?

Where Will I Work?
AJAC has partnered with 300+ advanced manufacturers to provide supervised, structured, paid on-the-job training.
AJAC apprentices can only work for companies that agree to hire them and place them into the program.
Each company has their own methodology for who they select as an apprentice.

Where Are Classes Held?
Classes are held one night a week, typically on a Tuesday, Wednesday, or Thursday from 5:00 pm to 9:00 pm.
AJAC’s apprenticeships classes are structured for both online learning or in-person learning. Depending on the specific class you are taking, you may be required to complete it online or in-person.
In-person classes are held either a local community/technical college, high school, or skills center.
Apprenticeship Classes
Operations Specialist apprentices take six college-level classes. Each class consists of 50 hours of lecture and/or practical application. Upon completion of each class, apprentices will receive 5 college credits.
As a registered apprentice, you automatically receive 50% reduced tuition. Over half of AJAC’s partnering employers elect to pay for their apprentice’s tuition, making the entire apprenticeship free-of-cost.
Currently, each class costs $380 out-of-pocket.
Students will be able to analyze capacity, demand, equipment, inventory, staffing, and budget reports. They be able to compose budgets for staffing, materials, and funding resources. They will gain a more in depth understanding of how to schedule staff, project tasks, procurement needs, and financial resource needs. Students will explain how production plans are built, including tools for prioritization and contingency planning. Students will learn best practices related to scheduling, estimating costs, forecasting workload, planning resource use, setting department goals, and monitoring progress. They will engage in effective debriefing communication to maintain continuous improvement of processes. 5 hours of safety in this course.
Apprentices are introduced to basic communication concepts relating to the workplace. Concepts include theory and skills practice related to interpersonal, intercultural, and production team communications, technical writing and business communications, phone and email etiquette, and conflict management. Students will create a professional portfolio that includes a resume, examples of skills, accomplishments, and samples of work.
In this course, students will be able to relate LEAN Six Sigma concepts to production objectives. They will identify waste within the value stream and demonstrate the ability to effectively analyze and present data to co-workers and stakeholders. They will define and apply team leadership tools to aid in process improvement. Students will collect and process customer or internal stakeholder input/requirements and identify key metrics for measuring success. Students will define the DMAIC process and effectively use tools and concepts associated with each phase of the DMAIC process. Finally, they’ll employ Lean Six Sigma skills in process improvement projects.
Students will develop tools to identify and communicate the evolving purpose of their organization. They will be able to provide guidelines to develop team unity towards that purpose. Students will adopt skills to empower team members and lead them to personal and professional growth. They will use planning tools to help manage change and work toward continued positive results. Students will explain and practice leadership best practices, including mentorship, creating specific and evolving goals, creating a work culture aligned for success, motivation techniques, and conflict resolution. This course introduces interpersonal communication skills critical to leaders, including running effective and productive meetings, developing active listening skills, contributing to group decision making, and strategies for presenting to a hostile audience. 5.5 hours of safety in this course.
Enterprise Resource Planning (ERP) refers to a method or type of software that organizations use to manage day-to-day activities. In this course, students will explore ways that ERP is used to efficiently manage demand and procurement. They will explain how ERP is used to quantify resource use, and better plan production jobs and product delivery. Students will use ERP to create invoices to send directly to customers or create and transmit import and export documentation required for cross-border shipments. Students will also identify how ERP processes enhance collaboration between businesses and vendors, helping to reduce bottlenecks. Students will explore how ERP use can help target inefficiencies in resource use and improve business outcomes. Finally, students will explain how ERP can help organizations adapt during business downturns. 3.5 hours of safety in this course.
Students will build on their knowledge of project management and explore techniques for getting projects back on track. They will focus on assigning project roles and responsibilities, problem solving, and risk management. Students will gain an understanding of tools and processes to help complete project on time and within operation production goals. This course will include some real examples of project management challenges being experienced by their classmate and the class will explore ideas to address those challenges. Students will recognize the importance of their roles as mentors to teach their teams problem solving skills. They will explore the concept of root cause analysis for identifying problems. They will practice ways to prioritize, plan, and efficiently solve problems once they have been identified. Students will be introduced to several methods of problem solving and explore one in detail. 5.5 hours of safety in this course.
On-the-Job Training Competencies
The table below is a schedule of tasks and hours designed as a guide. The 3,000 hours will be completed over the course of the apprenticeship. The apprentice shall be instructed and trained in all operations and methods customarily used on the various machines. Each company will adhere to the schedule as closely as facilities will permit in order to provide the apprentice with well-rounded experience and practice on all relevant equipment and processes in the shop.
OJT Competency | Approx. OJT Hours |
---|---|
Monitors and builds daily production goals | 1,000 |
Conducts continuous improvement meetings and projects | 800 |
Directs and aids line production staff in daily tasks | 600 |
Performs operational trainings on production equipment | 300 |
Supports internal and external quality assurance programs | 300 |
TOTAL HOURS | 3,000 |
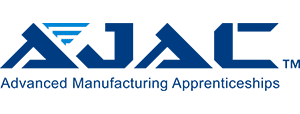
Launch Your Career Today!
Submit your information using the link below. After we receive your information, an AJAC representative will contact you for next steps. Please note, this is not an official application to become an apprentice. After a partnering employer agrees to enroll you in the program, you will officially apply and enroll at that time.